Quality Practice Area
Driving positive change by delivering quality-focused solutions that add value to the business.
Our team of quality professionals brings years of experience and expertise within the Life Sciences industry. We will work with you to assess your needs and design a customized solution for your organization while leveraging industry best practices and proven methodologies. Throughout the process, we will partner with Enterey’s team of experienced project managers and solutions applications to ensure successful project delivery, outcomes, and the sustainment of positive change.
Scope of Services
Driving positive change by delivering quality-focused solutions to achieve your business goals
Quality Strategic Planning
- Quality strategic plan development
- Strategy deployment
- Quality gap and maturity assessments
- Future focused QA/QC roadmaps
- Digital transformation
- Project portfolio management
- Change management
Quality Systems
- Quality documentation
- Electronic Quality Management System (QMS)
- Quality performance metrics and dashboards
- Quality business process models
- Inspection readiness
- Internal/external audits
GMP Training
- Learning framework
- Training plans
- Electronic Learning Management Systems (LMS)
- GMP capability building
- Training effectiveness
Quality Risk Management
- QRM procedures and toolkits
- Quality risk logs
- Facilitation of risk management process
- QRM training and capability building
Interim Quality Leadership
- Interim quality leadership roles
- Tactical resource augmentation
Our Product Options
Enterey can tailor a package to meet your needs, here are some examples of products that may help you decide the level of support you require.
Ongoing Support
Comprehensive
Our Enterey Quality professionals have the expertise, experience, and flexibility to immediately impact your organization. From leading strategic transformational change initiatives to providing tactical execution as members of your quality team, we can help you achieve your business goals.
Change Partner
Enterey collaborates with you to develop and implement:
- Quality strategic plans
- Quality system documents
- Quality processes
- Electronic quality systems
- Quality risk management processes and programs
- GMP Training programs
- Quality metrics dashboards
Ad Hoc Support
Quality Assessments
Short engagements to assess:
- Compliance to phase appropriate health authority regulations & expectations
- Quality system health
- Data integrity of your systems
- Inspection & launch readiness
- Quality Quality Management Maturity (QMM)
- Quality organizational design
Improvement Roadmaps
Development and execution of roadmaps to:
- Drive improvement to your quality systems
- Remediate compliance gaps
- Ensure data integrity of systems and processes
- Ensure inspection readiness
- Improve your Quality Management Maturity (QMM)
- Achieve digitalization and improve visibility of quality data
Bringing Expertise to the Table
Experience you can count on: Our team of experienced Quality professionals will work with you to assess the current state of your quality system and evaluate your current challenges. We will work with you to develop a plan and roadmap to close gaps, remediate deficiencies, improve your quality systems and processes, address risks, or evolve your organizational quality maturity.
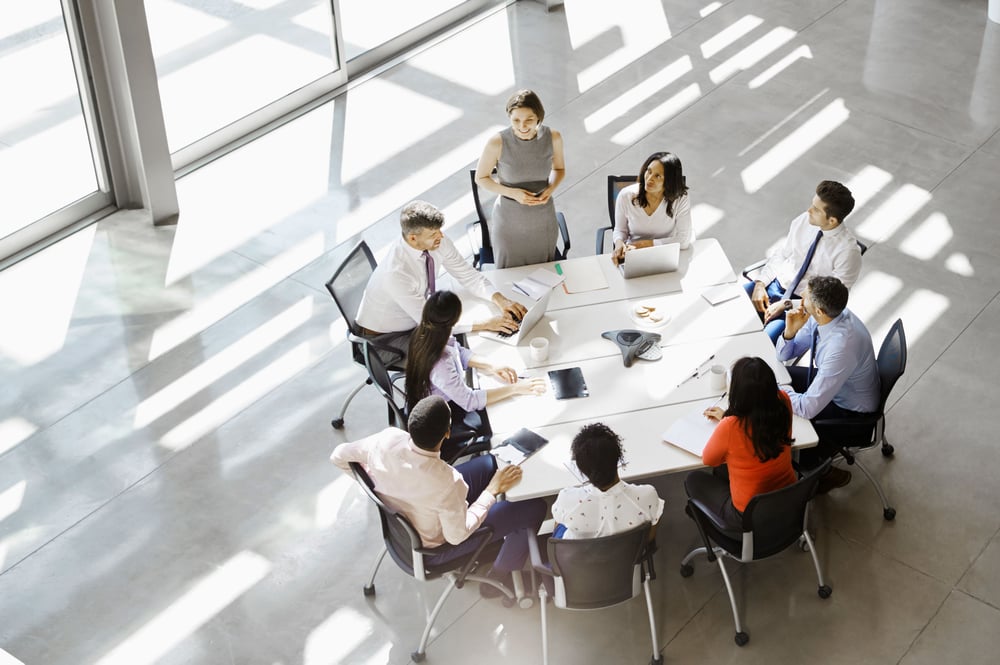
Consultants with extensive Quality expertise within the industry. When you partner with us, you have support from the whole Quality Practice Area Team!
Customized solutions to meet your specific needs, while leveraging industry best practices.
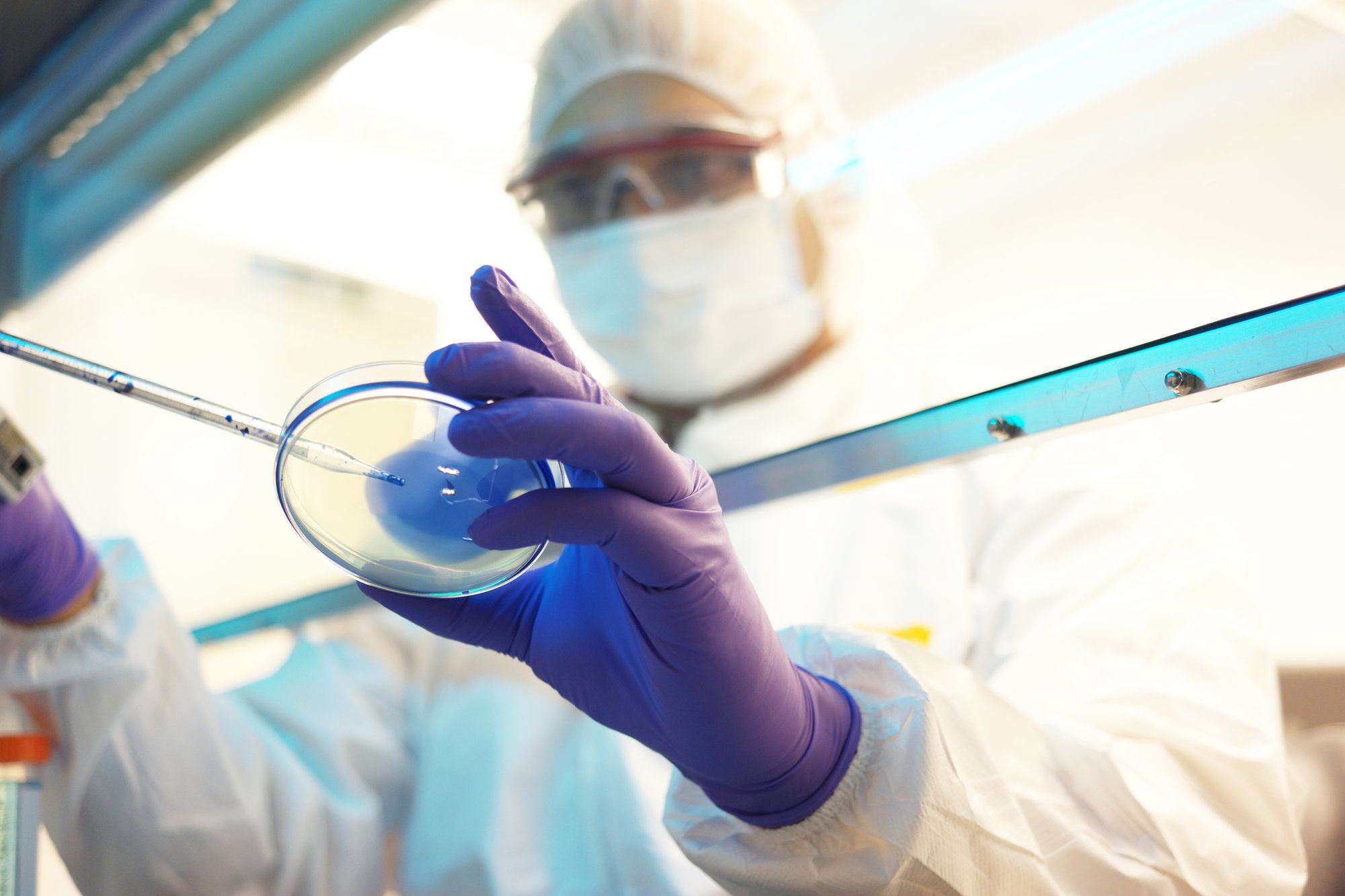
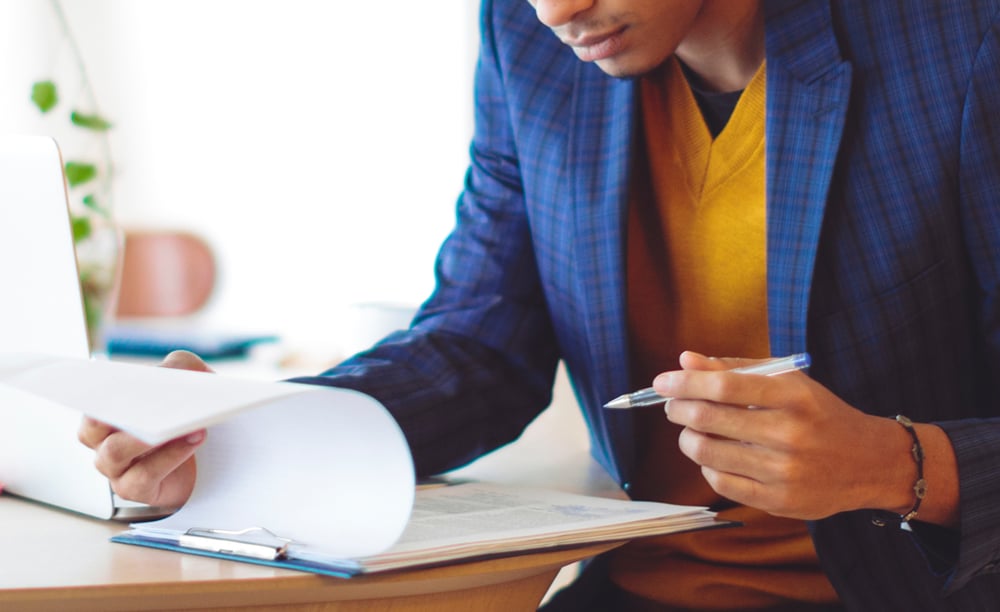
Partnership with Enterey’s team of experienced project managers and solutions applications to ensure successful project delivery and outcomes.
Our Process
- Understand your challenges and define the problem
- Assess the current state
- Design future state
- Develop the plan and roadmap
- Implement the solution
- Sustain the change
Example Case Studies
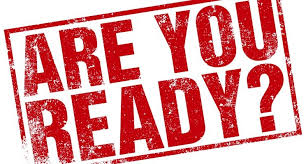
Inspection Readiness
Following the completion of construction and plant commissioning, our client set timelines to license its new facility and to pass all the required inspections, including State, FDA, and EMEA Pre-Approval Inspections. The project goal was to ensure the new facility met these inspection criteria.
Discovery & Design
Enterey consultants performed a gap analysis and provided action plans to remediate or defend the gaps identified in the plant’s Quality System.
Implementation
Our team provided project management support to the 14 departments throughout the plant and the Director of Quality Assurance. In addition, our team ensured regular communication by providing updates to Corporate Compliance and the GMP Core Team. Enterey consultants also supported the staff during the inspections regarding defense strategies, documentation, and final inspection room preparation.
Results Achieved
Our client’s facility was licensed as planned, and the State, FDA, and EMEA inspections succeeded. Only minor observations were issued by the State and EMEA, while there were no FDA observations. Action plans to correct the minor observations were timely and successfully implemented.
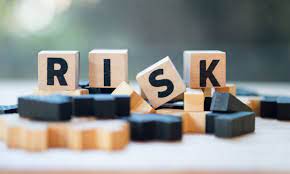
Risk Management
Following an assessment of their risk management processes, our client evaluated these to be inadequate because risks were not being addressed within reasonable timeframes. The significant backlog of unresolved risks resulted from unclear processes and a lack of consistency in identifying and implementing solutions.
Discovery & Design
Enterey consultants performed Voice of Customer assessments and facilitated workshops to redesign the process with clear actions and sustainable triggers.
Implementation
Our team provided templates and tools to standardize risk scoring and prioritization and plan resource requirements by applying the lean concept of capping Work in Progress. To facilitate the implementation of the process, our team also created tools to increase visibility and revolutionize the tracking of risk performance indicators.
Results Achieved
Our client experienced an unprecedented improvement in process performance consistency and communication, with over 50% of the open risk backlog being closed within six months of implementation. This project received formal recognition from the client for successful process improvement.