Artificial intelligence (AI) and interconnected technologies are increasingly accepted in business a...
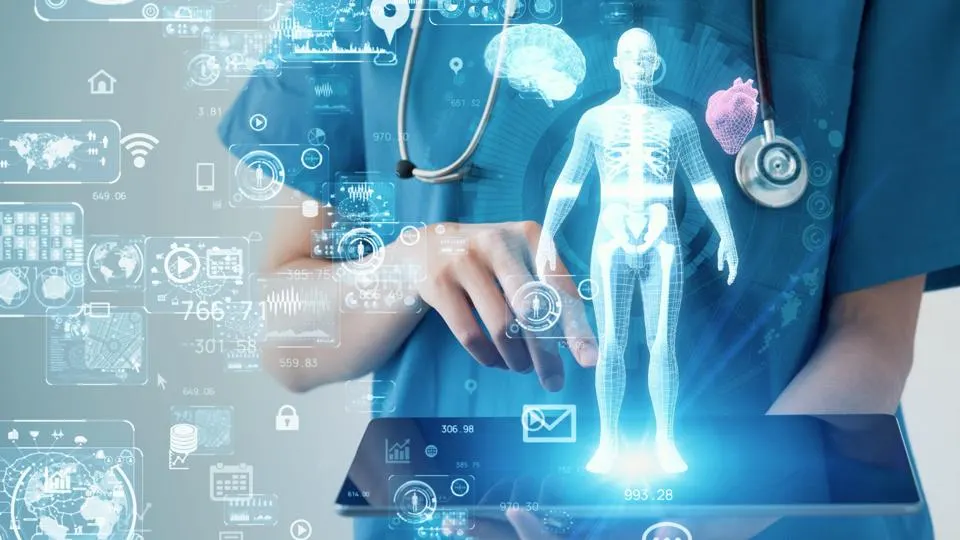
Enter Search Inquiries Below
Artificial intelligence (AI) and interconnected technologies are increasingly accepted in business a...
We are collecting a lot more health data today than we have in the past, but turning all those data ...
Integrated care is vital to patients, meaning we need systems that communicate with each other so pr...