Operationalizing a Manufacturing Facility: Pioneering the Future of Healthcare
Cell and gene therapies are revolutionizing healthcare by using living cells and genes to
treat various diseases. Cell therapy involves manipulating cells to restore damaged
tissues, while gene therapy modifies genetic material to combat genetic disorders. The
benefits of these therapies are immense, from offering potential cures and personalized
treatments to minimizing side effects and extending lives. However, to ensure these
therapies are safe and effective, strict adherence to Current Good Manufacturing Practices
(cGMP) is essential. At a minimum, cell and gene therapy manufacturing facilities are
governed by FDA’s guidance documents and regulations such as 21 CFR Part 210, 211, and
1271, as applicable. Additional requirements may be required depending on the nature and
scope of the project.
cGMP requirements serve as a cornerstone for the pharmaceutical industry, encompassing
guidelines and regulations that ensure drug products' quality, safety, and efficacy.
Compliance with GMP standards is crucial in all stages of drug development, from research
and development to commercial manufacturing. Among others, key aspects of GMP
requirements include facility design, equipment qualification, process validation, personnel
training, and documentation.
Ensuring operational readiness is a critical step in the commissioning and start-up of a new
manufacturing facility. Operational readiness refers to the state of preparedness of the facility, equipment, and personnel to begin full-scale manufacturing operations. The following are some ways to ensure operational readiness.
-
Facility and Technology Readiness: One of the most important things that get read before GMP manufacturing is having the facility in a desired state and the technology set up correctly. To achieve this, it is vital to efficiently design and qualify the facility while ensuring that procedures are in place for cleaning, disinfection, and decontaminating the facility to ensure that it is free from contaminants, such as airborne particles, bacteria, and viruses. With many facilities now leveraging single-use technology (SUT), this single-use design must be qualified to meet the process requirements.
-
Equipment Commissioning, Qualification, and Validation: All manufacturing equipment must be installed, qualified, calibrated, and validated, as applicable, to ensure that it operates within the required specifications. Equipment should also be tested for functionality and reliability by performing a qualification, and any issues should be resolved before full-scale operations begin. Regular maintenance of this equipment is equally essential to maintaining the manufacturing facility.
-
Effective Standard Operating Procedures (SOPs): SOPs should be developed for each stage/step of the manufacturing process. SOPs ensure consistency in running an equipment/unit process and that each process is conducted according to predefined standards.
-
Personnel Training: Personnel should be trained on the manufacturing process, SOPs, quality control measures, and safety procedures. Training should be comprehensive and conducted by experienced trainers. Personnel should also be trained on how to respond to potential manufacturing disruptions.
-
Process Validation: The manufacturing process should be validated to produce products that meet quality standards consistently. Validation studies should be conducted to verify this consistency.
-
Regulatory Compliance: The manufacturing facility should comply with all regulatory requirements and guidelines. This includes regulatory inspections, developing a Quality Management System (QMS), and adherence to Good Manufacturing Practice (GMP) standards.
Overall, operational readiness is critical to ensure the successful start-up of a new
manufacturing facility. The facility can be prepared for full-scale manufacturing operations by implementing the above steps, and production can begin safely, efficiently, and with
high-quality products.
TOGETHER
WE WILL TACKLE
YOUR TOUGHEST
PROBLEMS
At Enterey, we believe you deserve the support required to get the job done right—and be
recognized for your leadership. We partner with life science organizations to
promote sustainable change that reduces costs and improves compliance over the long haul.
Our people-first approach means that we’ll build authentic relationships, uncover truths,
and develop the best solution. To learn more, schedule a call with us using the link here.
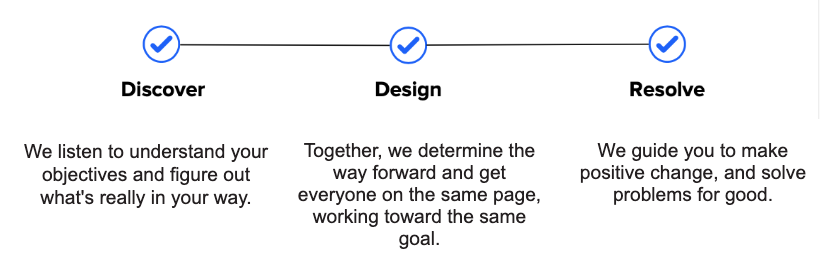
You can find more blogs here.