Patient distrust in hospitals and corporations to protect their personal data is a challenge to coll...
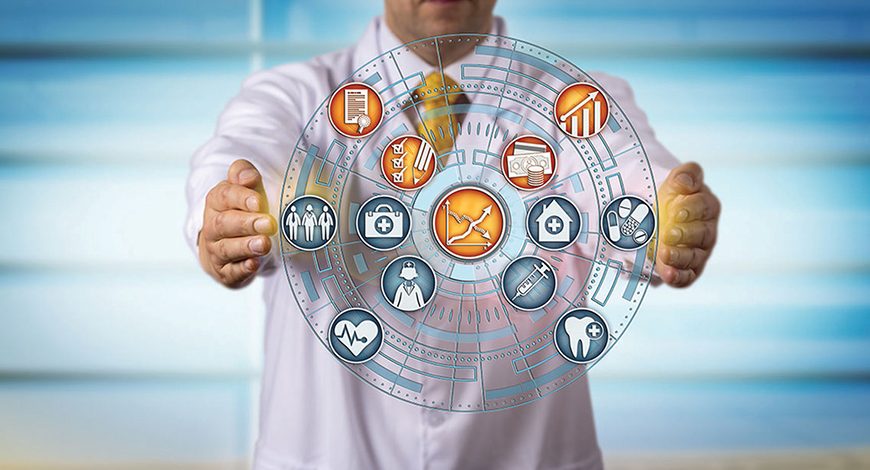
Enter Search Inquiries Below
Patient distrust in hospitals and corporations to protect their personal data is a challenge to coll...
Hospitals are still understaffed after the COVID-19 pandemic and are always looking for ways to stre...
Breakthroughs in health tech and patient care are irrelevant if patients can’t use them. We must enh...
Artificial intelligence (AI) and interconnected technologies are increasingly accepted in business a...
We are collecting a lot more health data today than we have in the past, but turning all those data ...